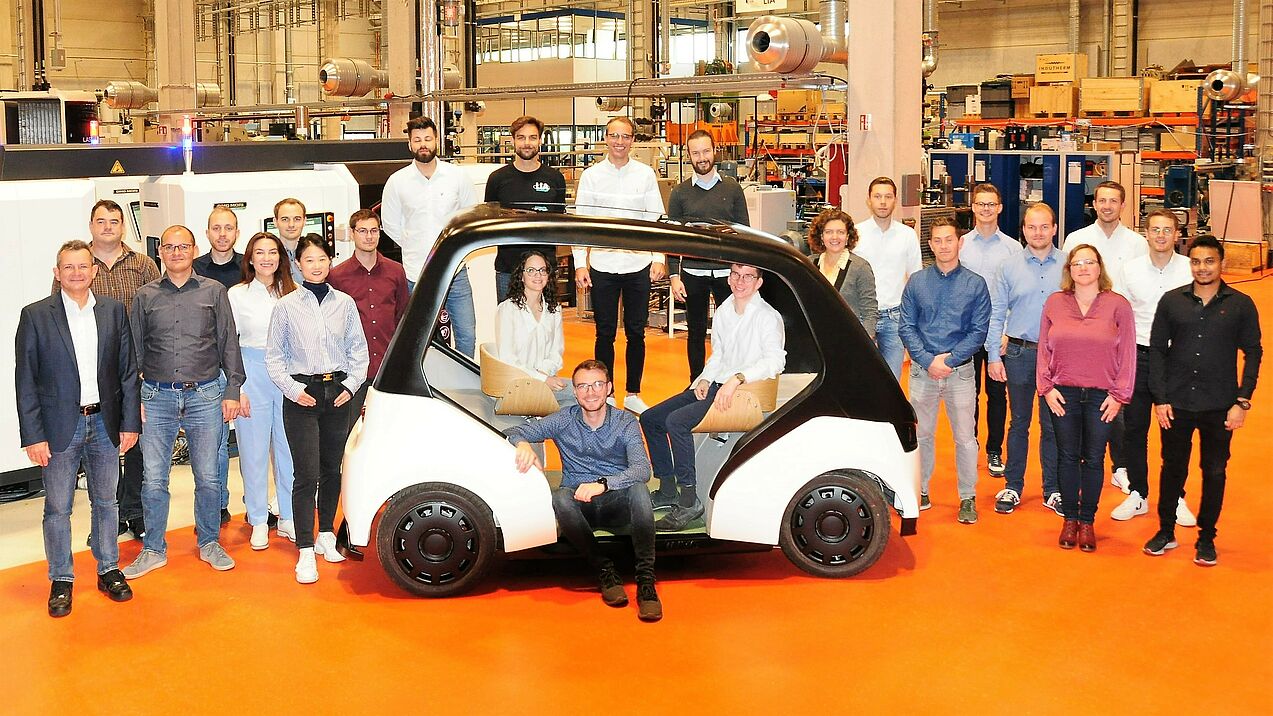
Die Knappheit natürlicher Ressourcen und die Reduzierung von Energieverbräuchen und der damit verbundenen Reduktion von klimaschädlichen Treibhausgasen sind aktuelle globale Herausforderungen und erfordern neue Lösungskonzepte um die internationalen Klimaschutzziele erreichen zu können. Der Leichtbau spielt hierbei eine bedeutende Rolle, da durch die Massereduktion bewegter Körper sowohl der Energieeinsatz als auch der Ressourceneinsatz minimiert werden kann. Im Bereich der straßengebundenen Mobilität z.B. führen Leichtbaumaßnahmen zur Senkung von Fahrwiderständen im Betrieb und somit zur Reduktion des Kraftstoffverbrauchs oder aber zur Reichweitenerhöhung eines batterieelektrisch angetriebenen Fahrzeugs.
Die Fachgruppe Leichtbau im Automobil (LiA) befasst sich daher mit innovativen Lösungen für den automobilen Leichtbau. Die Forschung fokussiert sich dabei auf die Bereiche der Simulation und Methodenentwicklung sowie der Werkstoff- und Prozessentwicklung von neuartigen Leichtbaulösungen. Diese können sowohl aus einzelnen Materialien bestehen (z.B. hochfeste metallische Werkstoffe, Faserverstärkte Kunststoffe FKV) als auch werkstoffkombiniert als Hybrid ausgelegt werden oder aber mit Hilfe der additiven Fertigung aus Pulvermaterialien hergestellt werden.
Forschungsschwerpunkte
Um die zentralen Herausforderungen von Funktionalität, Ressourceneffizienz, Nachhaltigkeit und Umweltverträglichkeit von Produkten und Produktionsprozessen in Zukunft sicherstellen zu können ist eine ganzheitliche Sichtweise auf Forschungsfragen wichtig. Die Forschungsaktivitäten in den einzelnen Domänen am LiA reichen daher von der grundlagenorientierten Forschung, in der Einzelaspekte einer Leichtbaulösung fundamental untersucht werden, bis hin zur anwendungsorientierten Forschung zur Gestaltung und Validierung späterer Prozesse und Produkte. Fachlich gliedern sich die Schwerpunkte der Forschung in 3 übergeordnete Teams am LiA.
Simulation & Methodenentwicklung
Das Team Simulation und Methodenentwicklung beschäftigt sich mit der Modellierung und Analyse komplexer mechanischer Systeme, deren Herstellverfahren und der Bilanzierung der Umweltbelastung. Je nach Detaillierungsgrad des Forschungsthemas werden Simulationsansätze auf der mikro- oder der makromechanischen Ebene durchgeführt. Für ein umfassendes Verständnis des mechanischen Verhaltens eines Bauteilkonzeptes stehen die sorgfältige Bestimmung der Randbedingungen und die Formulierung von Materialmodellen im Vordergrund. Dadurch kann eine realitätsnahe und zuverlässige Simulation durchgeführt werden, in der die in realen Anwendungsszenarien auftretenden Lasten berücksichtigt sind und entstehende Wechselwirkungen bestimmt werden. Für die Erstellung von Materialmodellen findet eine umfangreiche experimentelle Charakterisierung der Werkstoffeigenschaften (z.B. von den eingesetzten Leichtbauwerkstoffen Aluminium, hochfester Stahl, Holz, CFK, GFK, etc.) an den Prüfmaschinen des Lehrstuhls statt.
Die Simulationsansätze umfassen neben den statischen impliziten Simulationen von einzelnen Bauteilen, Modulen oder aber Gesamtstrukturen auch die für die Automobiltechnik wichtigen expliziten Simulationsansätze im Bereich Crash. Hierdurch können Spannungs- und Dehnungsverteilungen innerhalb der Bauteilkomponenten bis zum Beginn des Versagens prognostiziert werden. Parallel dazu entwickelt und untersucht das Team Algorithmen, die speziell für die Schädigungs- und Versagensmodellierung eingesetzt werden. Diese Algorithmen dienen zur Vorhersage des Beginns und des Fortschreitens der Materialschädigung innerhalb der Bauteile und können z.B. Resttragfähigkeiten der Bauteile prognostizieren.
Ein weiterer Forschungsschwerpunkt des LiA im Bereich Simulation stellt die Auslegung und Simulation von Verbindungstechnologien (mechanisch und stoffschlüssig) oder aber der entsprechenden Herstellprozesse der Bauteile dar. Dies ist unabdingbar bei der Entwicklung und Belastungsanalyse von Baugruppen und Gesamtfahrzeugstrukturen. Dies gilt insbesondere wenn der Herstellprozess direkte Auswirkungen auf die späteren Bauteileigenschaften (z.B. Gefügeänderungen oder aber Kaltverfestigung metallischer Werkstoffe während des Fertigungsprozesses) hat.
Die Kalibrierung und Validierung der Simulationsansätze wird durch umfangreiche Analysen und Vergleiche zwischen den simulierten und den experimentellen Ergebnissen erreicht, wodurch eine valide Aussagefähigkeit der Forschungs- und Entwicklungsergebnisse sichergestellt werden kann.
Parallel zur funktionellen Auslegung und Entwicklung ist das Team des LiA in der Lage Nachhaltigkeitsbewertungen von Leichtbaulösungen z.B. durch eine Lebenszyklusanalyse (LCA) durchzuführen. Ziel ist es dabei die Umweltauswirkungen der Leichtbaukonzepte bereits in der frühen Entwicklungsphase möglichst genau zu bewerten, um die Entscheidungsfindung bei der Auswahl von Materialien und Verfahren zu verbessern. Damit trägt das Team zur Entwicklung von Leichtbaulösungen bei, die den technischen, wirtschaftlichen und ökologischen Herausforderungen gerecht werden.
Innerhalb des Teams Werkstoffe und Prozesse wird ein Fokus auf die Prozessierung von Werkstoffen mit einem hohen Leichtbaupotential gelegt. Dieses ist gegeben, wenn der Quotient aus Festigkeit bzw. Steifigkeit und Dichte des Werkstoffs maximiert wird. Relevant sind daher hochfeste Stahl-, Aluminium- und Titanlegierungen sowie Faserverstärkte Kunststoffe (FKV). Je nach Anwendungsfall kann es besonders vorteilhaft sein, wenn unterschiedliche Werkstoffe miteinander kombiniert werden. Derartige Hybridverbünde vereinen die jeweiligen Vorteile der Werkstoffe und kompensieren werkstoffspezifische Nachteile.
In der Analyse der jeweiligen Fertigungsprozesse soll neben der Maximierung der mechanischen Eigenschaften der solitären bzw. hybriden Werkstoffsysteme eine nachhaltige und energieeffiziente Verarbeitung sichergestellt werden. Dazu werden spezielle Methoden zur Erwärmung (z. B. Induktion, Konduktion) oder aber eine Kombination von Prozessschritten (z. B. In-Mold-Assembly (IMA)) eingesetzt. Entsprechende Optimierungen werden zunächst im Labormaßstab an kleineren Probenkörpern analysiert und auf Basis realitätsnaher Demonstratoren hochskaliert. Unterstützt wird die Prozessforschung durch den Einsatz geeigneter numerischer Methoden (z.B. Umformsimulationen, Füllstudien). Eine Validierung der durch den Prozess resultierende Eigenschaften kann u. a. über bildauflösende Verfahren (Mikro – Makroebene) und mechanische Prüfungen sichergestellt werden.
Die Forschungsschwerpunkte im Bereich der Additiven Fertigung liegen im Prozess- und Bauteildesign. Hinsichtlich des Prozesses liegt die Parameterentwicklung und die Prozessoptimierung im Fokus. Unterstützt durch Qualifizierungen der mechanischen Eigenschaften und Mikrostrukturanalysen werden die Prozesse verbessert, um die Qualität und Leistung der hergestellten Bauteile und auch die Effizienz und Nachhaltigkeit des Prozesses zu maximieren. In Bezug auf das Bauteil werden Topologieoptimierungen und Simulationen eingesetzt, um optimale Strukturen zu entwickeln. Dies ermöglicht die Herstellung leichter, robuster und effizienter Bauteile. Durch den Einsatz von Simulationen können verschiedene Designkonzepte vor der physischen Fertigung getestet und optimiert werden, was Zeit und Kosten einspart und zur effizienteren Fertigung führt. Insgesamt trägt die Forschung des Teams Additive Fertigung dazu bei, die Möglichkeiten und Grenzen dieser fortschrittlichen Fertigungstechnologie zu erweitern und neue Anwendungen in verschiedenen Branchen der Mobilität zu erschließen.
Ausstattung
In Bezug auf die technische Ausstattung besitzt der Lehrstuhl für Leichtbau im Automobil verschiedenste Möglichkeiten und Prozessketten zur Herstellung von Demonstratoren und Bauteilen und zur Charakterisierung von Materialparametern sowie der Eigenschaften der hergestellten Bauteile. Dabei kann ein breites Spektrum an statischen, zyklischen und dynamischen Tests sowie mikrostruktureller Untersuchungen durchgeführt werden. Neben 3-Achs-Prüfungen mit statischen und zyklischen Kräfte bis zu 80 kN können auch Tiefungsversuche mit Temperaturen von bis zu 800°C und Hochgeschwindigkeitszugversuche durchgeführt werden. Zudem besitzt der Lehrstuhl eine Komponenten-Crashanlage, an der Crash-Versuche mit Aufprallgeschwindigkeiten von bis zu 25 m/s und Schlagenergien von bis zu 31 kJ erreicht werden können. Die Testergebnisse können mit Hochgeschwindigkeits-3D-Kamera-Systemen analysiert werden um zum Beispiel lokale Dehnungs- oder Temperaturverteilungen während der einzelnen Versuche bestimmen zu können.
Darüber hinaus nutzt der Lehrstuhl für Leichtbau im Automobil verschiedene CAD- und Simulationswerkzeuge, wie Siemens NX, Solidworks, Abaqus, LS-Dyna und Hyperworks und kann seine Berechnungen auf dem Hochleistungsrechner Noctua 2 der Universität Paderborn durchführen.